Para empezar deberíamos saber que hace un equipo de soldadura, el proceso de la soldadura consiste en unir dos piezas empleando calor hasta que se consiga su fusión , consiguiendo así la unión del metal fundido con las piezas.
Tradicionalmente el método para soldar que mas se usaba en la reparación de carrocerías ha sido la soldadura oxioacetilénica, un que en la actualidad esta casi en desuso, y esto es debido a lo lento que es el proceso y por los cambios estructurales que se producen en los metales al someterlos a las elevadas que produce este equipo de soldadura.
Frecuentremente también se llama a este proceso "soldadura autógena" y esto es por que el material de las piezas a unir y el metal de aportación(en caso de que se use)son de la misma naturaleza.

Esta soldadura consiste en llevar hasta la temperatura de fusión los bordes de la pieza a unir. MedianTe el calor producido por la llama oxiacetilenica que se el resultado de la combustión de un gas combustible , el acetileno , mezclado con un gas comburente como es el oxigeno. Estos gases se mezclan y se dosifican en un soplete, por cuya salida se produce una llama oxioacetilenica que puede llegar a alcanzar los 3000º.
Con este tipo de soldadura se pueden soldar distintos materiales , como el acero,latón,cobre,aluminio,magnesio , fundiciones y sus aleaciones. En ocasiones también se puede usar otro combustible como el hidrógeno,propano, gas natural o cualquier otro combustible, aunque tienen un inconveniente respecto al gas acetilenico y es que no alcanzan temperaturas tan altas como con acetileno.
Para el uso de la soldadura oxiacetilenica se necesita un equipo especifico que costa de los siguientes elementos:
- Botella de acetileno
- Botella de oxigeno
- Soplete
- Válvula de seguridad
- Mangueras
- Manorreductores
Botella de acetileno
Las botellas de acetileno se suministran en botellas de acero estirado, a una presión de unos 15 kg , aunque en la actualidad exiten equipos portables con menos capacidad.Como ya hemos dicho se usan botellas de cierre hermético, este tipo de botellas también se usan para contener gases y líquidos muy volátiles.
Partes del cilindro:

Tapa: el objetivo de esta pieza es proteger la válvula del cilindro, pudiendo ser fija o removible.
Válvula: es la que se encarga de dejar o no el paso del gas, fabricada en la mayoría de los casos con latón forjado, esta diseñada para trabajar con gases en altas presiones.
Collarín: pieza fijada ala garganta y provista de una rosca externa para la colocación de la tapa.
Garganta: parte gruesa del cilindro dispuesta hacia afuera en dirección de su eje, en la cual existe un orificio roscado para la colocación de la válvula.
Hombro: parte del cilindro donde cambia el radio del cilindro, es decir donde pasa del cuerpo a la garganta.
Cuerpo: es la parte que mas ocupa , y se diferencia de las demás partes por que todas los puntos de sus paredes están a la misma distancia de centro es decir tienen el mismo radio
Base: parte del cilindro de una configuración que permita la estabilidad del mismo en posición vertical.

Botella de oxigeno
Al igual que las botellas de acetileno se suministra en botellas de acero estirado a una presión de unos 200 kg, también se consiguen en equipos portatiles mas pequeños.
La estructura de las botellas de oxigeno es igual a las de acetileno, válvula , collarín , garganta...
Al ser intensamente oxidante, deberá evitarse todo contacto con sustancias fácilmente combustibles, ya que podrá provocar su combustión. Todos los accesorios y elementos que puedan entrar en contacto con el oxígeno deberán estar exentos de grasa, aceites y lubricantes.

El soplete
El objetivo de estos de estos dispositivos es mezclar los gases (en este caso sera oxigeno/acetileno) para conseguir el tipo de combustión deseada.
El soplete costa de diferentes partes como ahora explicaremos, en la parte central lleva el dispositivo mezclador de los gases que por medio de unas llaves, se regula la cantidad de uno y de otro gas que se necesita para formar la mezcla de salida , esta zona se conoce como zona de mezcla, que a su vez es la zona del mango por donde se agarra el soplete.
La mezcla ya realizada sigue hasta la boquilla de salida a través de un tubo acodado conocido como "lanza".
Los sopletes tienen en su parte posterior las tomas donde van conectadas las mangueras que los unen con las botellas.
Los sopletes están equipados con un juego de boquillas calibradas que se identifican como ya enseñaremos mas adelante. A mayor numeración, mayor diámetro de salida y por tanto mayor caudal de gases.
En la reparación de las carrocerías se suele utilizar las boquillas del numero 0,1 y 2.
En la reparación de las carrocerías se suele utilizar las boquillas del numero 0,1 y 2.
Entre el soplete y las botellas , en ambas tomas , se conectan unas válvulas de seguridad antiretorno , esto se hace para evitar que la llama pueda entrar por la manguera y llegue a las botellas , lo que podría causar un gran accidente.
Este tipo de válvulas esta compuesta por un tubo poroso , por el que se desplaza en su interior un embolo que cuando el mecanismo esta en reposo obstruye el paso del gas, cuando se acciona la presión del gas vence la fuerza del muelle que esta en la parte posterior de la válvula permitiendo así el paso del gas por el interior de la válvula , atravesando el tubo poroso y sale al exterior en dirección a el soplete.
Si por un casual la llama retornase , aumentaría la presión en el embolo donde se encuentra el muelle , reforzando así vez la presión que se ejerce sobre el embolo y tapando completamente el paso del gas.
Existen dos mecanismos de seguridad en cada válvula como ya hemos visto , que han de funcionar perfectamente y que se deberían sustituir cada cierto tiempo o cuando se pueda creer que han fallado y ha retornado la llama en algún momento.
Las válvulas antirretorno se suelen instalar en la entrada de la empuñadura , ala salida del manorreductor o en la propia manguera.
Mangueras
Las mangueras son elementos flexibles, lisos por el interior construidos con múltiples capas una de ellas de goma sintética resistente a la acción de los gases,también suelen llevar mallas textiles para mejor la estructura de la manguera, y están cubiertas de una capa de goma sintética que suelen ser de color rojo para el acetileno y verde/azul para el oxígeno, resistente a la abrasión, a la luz y a los posibles agentes atmosféricos.
Las mangueras son los elementos que sirven de conexion entre los manorreductores y el soplete. La presión a la que pueden trabajar tiene limitaciones por lo que se deberá regular la presión en manorreductor para controlar en todo momento la presión de salida de los gases.
Los manorreductores
Los manorreductores son otro dispositivo del equipo de soldadura oxiacetilenica y se instalan en los grifos de botellas de oxigeno y acetileno.
La función de este dispositivo es suministrar gas a presión constante , sin depender de los cambios de presión que puedan ocurrir en la botella a medida que se va vaciando.
Esta compuesto por dos manómetros , uno de alta presión , donde se puede comprobar la presión que queda en la botella(es decir la cantidad de gas que queda), y otro de baja presión donde se comprueba la presión de utilización.
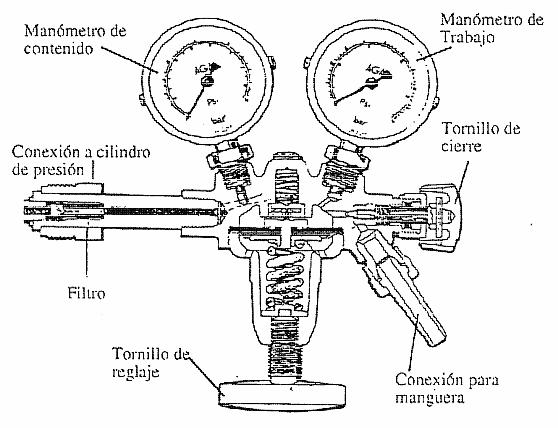
La presión se regula con la apertura y cierre de una aguja obturadora. El mecanismo de apertura y cierre está asegurado por una membrana flexible y dos muelles. Atraves de un tornillo de expansión el operario puede regular la presión de trabajo.
Ahora vamos a explicar su funcionamiento un como mejor:
Cuando la botella esta cerrada , no existe presión en el manorreductor, el tornillo de expansión se encuentra cerrado.
Al dejar pasar el gas de la botella al abrirla , el gas llega hasta la aguja obturadora, que se mantiene sobre su asiento por la accion del muelle que tiene en la parte superior , y el gas no pasa mas.
Cuando se rosca el tornillo de expansión ,esto hace que presione el muelle inferior , que este al comprimirse transmite la presión a la menbrana , esto hace que pase por el empujador , hace desplazar a la aguja obturadora y vence la resistencia del muelle superior, dejando así pasar el gas.
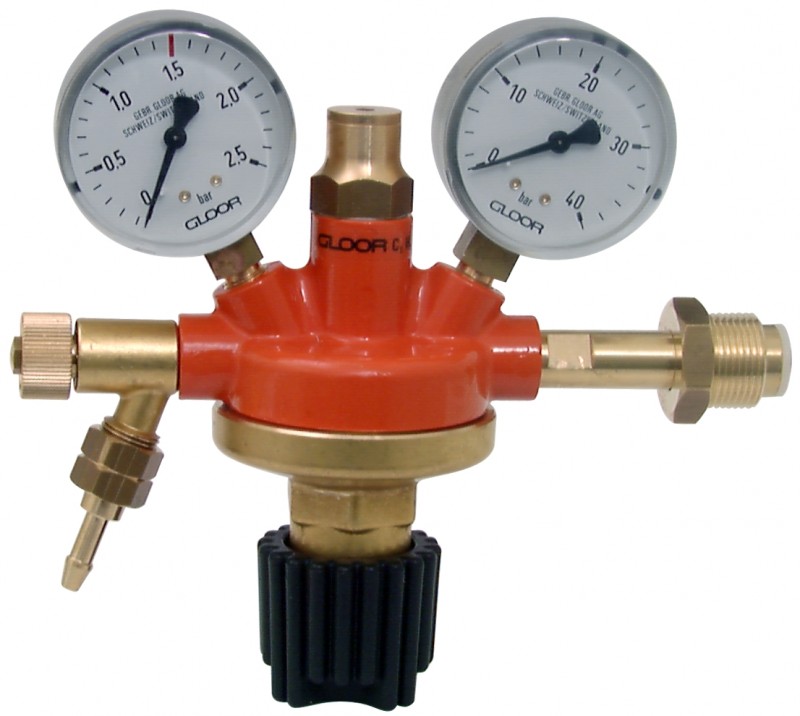
Al salir el gas por el soplete , la presión desciende este proceso se repite continuamente para regular la presión y que sea lo mas constante posible.
Existen unos manoreductores de doble cámara que consiguen una presión y caudal mas uniforme , evitando así variaciones durante la operación de soldeo.
Comburente
En este caso el comburente sera el oxigeno que es un gas incoloro, inodoro e insípido. Es el gas comburente ya que contiene la sustancia oxidante que , al reaccionar con otras sustancias combustibles, provoca su combustión.
El oxigeno es el comburente mas usado, se extrae industrialmente del aire o del agua. El aire atmosférico contiene sobre un 21% y se obtiene mediante una destilación fraccionada del aire líquido , mientras que el agua contiene un 89% y se consigue extrayéndolo por electrólisis.
Luego el oxigeno obtenido se comprime en botellas de paredes gruesas que se fabrican de acero estirado sin soldaduras y son sometidas a pruebas hidráulicas con presiones de 235 kg/cm2, aunque la presión con la que se suelen cargar es de 150 kg/cm2 a la temperatura de 20 º. Para los que no sabíais el metro cubico de oxígeno pesa unos 1,38 kg hay muy poca diferencia entre una botella vacía y una llena.


La ojiva (sobre la ojiva se encuentra el grifo ) se pinta de color blanco con las letras OX en negro. Además tiene indicado el nombre del fabricante , su dirección, año y numero de fabricacion, contenido en litros de agua y presión de la primera prueba . El cuerpo es de color negro.
Combustible
El gas combustible que se usa casi siempre es el acetileno , por eso vamos a hablar un poco de él. Para su elaboración se usa el carburo de calcio y el agua.
El carburo de calcio es un cuerpo solido que tiene el aspecto y la dureza de una piedra. Se consigue combinando carbono y cal en un horno eléctrico que produce una temperatura de unos 3000º.
El acetileno se obtiene por la reacción del carburo con el agua, el gas que se desprende es el acetileno, y tiene un olor peculiar, que proviene sobre todo del hidrógeno fosforoso. Es un gas incoloro , mas ligero que el aire y altamente inflamable.
El acetileno es un gas muy inestable , propenso a descomposiciones, hasta tal punto que en estado liquido se le considera explosivo y no debe ser comprimido a una presión superior a 1,5 bar .
Para su embotellado se disuelve en acetona que es el disolvente que tiene mas capacidad de absorción. Las botellas de acetilenose rellenan a una presión de unos 15 bar y con una temperatura ambiente de 15º.
El acetileno producido de forma industrial es envasado en botellas con paredes gruesas echas de acero estirado y sin ninguna soldadura. Para su identificacio , la botella se pinta de rojo, y en la paste superior de la botella o ojiva lleva estampado la indicación de " acetileno disuelto" , se pinta de color marrón.

Tipos de antorcha, boquillas, tamaños, tabla de regulación de caudales según boquilla…
La principal función de la antorcha es la correcta mezcla del flujo entre el comburente y el combustible. También otra de su función es guiar el gas hacia la boquilla .
Como ya hemos dico la antorcha o solete tiene an el lado contrario de la boquilla la entrada del oxigeno señalado como OX otra entrada para el gas acetilenico señalado como AC
Antorcha de corte tipo N se usan para soldaduras de oxígeno-acetileno y tipo H estas se usan para oxígeno-acetileno y oxígeno-propano.
Antorcha oxibutano: se utiliza para calentar elementos y se usa generalmente cuando el gas combustible es el butano.
Soplete de corte tipo Harris de palanca lateral, es recomendado para trabajos intensos de desguace y corte.
Soplete tipo Harris de soldeo son los mas extendidos ya que valen para la mayoría de cosas generalmente usados en chapistería, fontanería y equipos portátiles para oxígeno, acetileno y propano.
TIPOS DE BOQUILLAS
Las boquillas son la ultima parte por donde los gases inmediatamente antes de su combustión.Son fabricadas de metal no ferroso como cobre o aleación de cobre, el cual tiene alta conductividad térmica y su uso reduce el peligro de una fusión a altas temperaturas.Las boquillas se encarga de guiar la llama, en el extremo por donde sale la llama se pueden colocar diferentes boquillas , dependiendo de de si es fija o intercambiable
- Fijas: Este tipo de boquillas están unidas al el soplete, por lo que no se podrá cambiar.
- Intercambiables: Estas boquillas se pueden cambiar dependiendo de las necesidades del usuario, se une mediante una rosca al intercambiador.
Dentro de las boquillas intercambiables hay otras dos tipos de boquillas que nos interesa conocer como son las boquillas de soldar y las de corte
- Boquillas corte: Se usan generalmente para realizar cortes en el material, este tipo de boquillas lo que hace es tener una llama mas fina que calentara una zona mas reducida a una temperatura mayor .
- Boquillas de soldar: Este tipo de boquilla se usa para soldar dos piezas generalmente, este tipo de boquillas son mas anchas por lo que calentaran una zona mas ancha que las de corte, pero como es lógico se tardara mas tiempo.

Esta tabla muesta una indicaciones de que tipo de presiones y el tipo de boquilla que deberíamos usar dependiendo del espesor del material que se va soldar.
La llama oxiacetilenica
Se denomina llama a la combustión de una sustancia con el oxigeno . En este fenómeno se desarrolla luz y calor. Las llamas para soldar se consiguen variando la proporción de acetileno y oxigeno,
Una vez encendido el soplete y regulada la proporción de gases, en la llama oxiacetilenicae diferencian tres partes o zonas bien diferenciadas.
La primera zona esta inmediatamente a la salida de la boquilla , se le conoce como"dardo", Rodeando el dardo se ve una zona azulada , llamada"zona reductora" que es donde se alcanza la mayor temperatura mas o menos a 5 mm del dardo y se alcanzan temperaturas de hasta los 3000º. La temperatura de la llama va descendiendo a medida que se aleja del dardo. Los gases que se producen en esta zona protegen a la pieza que se va a soldar de la acción del aire atmosférico, como podía ser la oxidacion.
También existe una tercera zona mas amplia que las anteriores , que rodea la zona reductora, tiene como un color rojizo y se le conoce como penacho.
Proceso de encendido
Trabajar con uno de estos equipos conlleva unos riegos ya que se utilizan temperaturas muy altas y sustancias peligrosas por lo que se tienen que tener una serie de cuidados y precauciones.
Para llevar a cabo el encendido de la llama se debe seguir un proceso que nos ayude a evitar incidentes.
- Lo primero para empezar a trabajar sera colocar la boquilla adecuada según el espesor de la pieza que vamos a soldar.
- Abrir y cerrar con cuidado las llaves de paso tanto del oxígeno como del acetileno para eliminar los posibles
residuos y eliminar la dureza de las llaves causa de la estanqueidad de las
válvulas.
- Abrir los grifos de la botella.
- Regular los manorreductores, mediante los tornillos de expansión para obtener una presión de unos 0,3 a 0,5 bar para el acetileno y 1,5 a 2,5 bar para el oxigeno.
- Abrir un poco el grifo del oxigeno y regular con muy poco caudal para vitar la formulación de hollín durante el encendido de la llama.
- Abrir el grifo del acetileno e inflamar los gases empelando un mechero o la chispa que viene con el equipo de soldadura. Durante el encendido es preferible que el acetileno esté en exceso y que la llama despegue de la boquilla.
Regulación de la llama
Ahora que la llama ya esta bien encendida , lo próximo sera regular la llama dependiendo de nuestras necesidades.
Lo primero sera regular el caudal del acetileno, se alcazara un buen caudal abriendo progresivamente el grifo del acetileno, haciendo que la llama que al principio es larga y de contornos casi paralelos pase a ensanchar en sus extremos.
Al aumentar el caudal del oxigeno, la llama cambiara de aspecto, haciéndose mas blanca, sus extremos serán mas transparentes, la zona blanca y luminosa que sera el dardo disminuirá su longitud para tomar una forma mas redondeada.
Ahora se observa que el dardo esta bien regulado , ya que su contorno es limpio y luminoso. Esta llama es la que conoceremos como neutra y es la que se usara normalmente.
Cuando se aumenta aun mas el caudal de oxigeno y se sobrepasa la cantidad adecuada se obtiene un dardo mas pequeño , azulado y menos brillante, a esta llama la conoceremos como llama oxidante.
Con una llama oxidante se producen numerosas proyecciones y se produce un burbujeo blanco en la superficie de fusión .Esto es causa de que el material se oxida y quema el material basey el de aportación (si se usa).La oxidación que suele ser una problema también tiene ciertas ventajas , ya que la temperatura de la soldadura es mas elevada y la fusión se produce mas facilmente. Se usa sobre todo para cortar y para soldadura de cobre, ya que el aumento de temperatura , contra resta la gran disipación de calor que se produce por la elevada conductividad del cobre.
Hay un tipo de llama mas , la llama carburante, esta se produce al aumentar el porcentaje de acetileno en la mezcla, consiguiendo así un dardo mas largo que en la llama neutra y un penacho blanco y alargado. Con esta llama se produce un exceso de carbono , que endurece y hace mas frágil el material.
Este tipo de llama se usa sobre todo para recargar piezas de acero que resultan mas duras que el metal base y también para la soldadura de aluminio y sus aleaciones por la menor temperatura de la llama y la menor presencia de oxigeno.
Una vez que ya hemos regulado la llama a nuestro gusto empieza el proceso de soldadura para eso hay que acercar la boquilla a la zona de soldadura, mantenerla a 5 mm de distancia entre el dardo y la pieza a soldar.
Una distancia menor a la que hemos dicho antes podría llevar a una soldadura mas lenta y defectuosa, haciendo además que la boquilla se pueda obstruir con mayor facilidad por el desprendimiento de material durante el proceso de soldado. Y una separación excesiva haría que el proceso mucho mas lento y carburaria la zona soldada.
Procedimiento de apagado
Puede que no parezca importante pero el proceso de apagado también hay que seguir unas pautas.Si la operación de soldado se va a interrumpir solo durante unos minutos, bastara con cerrar los grifos del soplete. Primero el acetileno y despues el oxigeno. Si la parada es mas larga ,de un par de horas, es mejor cerrar también los grifos de las botellas.
Si se va aparar por un largo tiempo, se deberia desalojar la presión de los gases para no estropear los muelles de los manorreductoresy , por seguridad para evitar que se produzca una rotura se bedera cerrar de la siguiente forma.
Primero cerrar los grifos de las botellas y dejar salir los gases abriendo las llaves de regulacion del soplete , hasta que el manometro descienda a cero.
Aflojar los tornillos de expansión de los manorreductores y cerrrar las llaves de regulacion del soplete.
Medidas de protección y seguridad a cumplir en su manejo
Este equipo produce temperaturas muy elevadas y se usan sustancias peligrosas como es el acetileno.
por eso hay que seguir unas normas de seguridad.- No utilizar herramientas que no sean las adecuadas para manipular el equipo.
- Evitar los golpes en general , pero sobre todo en la zona de las llaves de regulacion.
- No desmontar una boquilla con el soplete todavia caliente.
- No engrasar los manómetros ni ningun elemnto del equipo, si fuera necesario usar jabon o glicerina.
- No utilizar una manguera que se haya usado para acetileno para el paso del oxigeno , ya que pueden quedar restos y es muy inflamable
- Realizar las conexiones de las mangueras y de los manorreductores con los metodos indicados por el fabricante.
- Tener siempre a mano unequipo de extincion de incendios que funcione correctamente
- Antes de empezar revisar el estado del equipo.
- No soldar cerca de recipientes que contenganproductor inflamables o que hayan podido contenerlos.
- Vigilar el salto de chispa y las proyecciones de material fundido
- Usar siempre los medios de preteccion personal.
- No consumir las botellas al 100%.
Aqui termina esta entada sobre la soldadura , espero que os haya servido de utilidad y que hayais aprendido algo, nos vemos en la proxima.
GRACIAS POR LA INFORMACION :V
ResponderEliminarMuy bueno
ResponderEliminarDisculpa, de donde conseguiste la tabla de presión y consumo de oxigeno y acetileno?
ResponderEliminar